The UGM series mining ultrafine grinding mill adopts advanced grinding technology, which can grind the ore into micron or even nano powder with extremely high grinding efficiency; its fully enclosed design can effectively reduce dust and noise pollution, reduce energy consumption in the production process, and meet environmental protection requirements.
Ultrafine grinding mills can freely set product fineness between 200 mesh and 2500 mesh for processing of minerals with humidity below 6%, non-flammable and non-explosive non-metallic materials with Mohs hardness below 9, and the finest can reach 3000 mesh or more.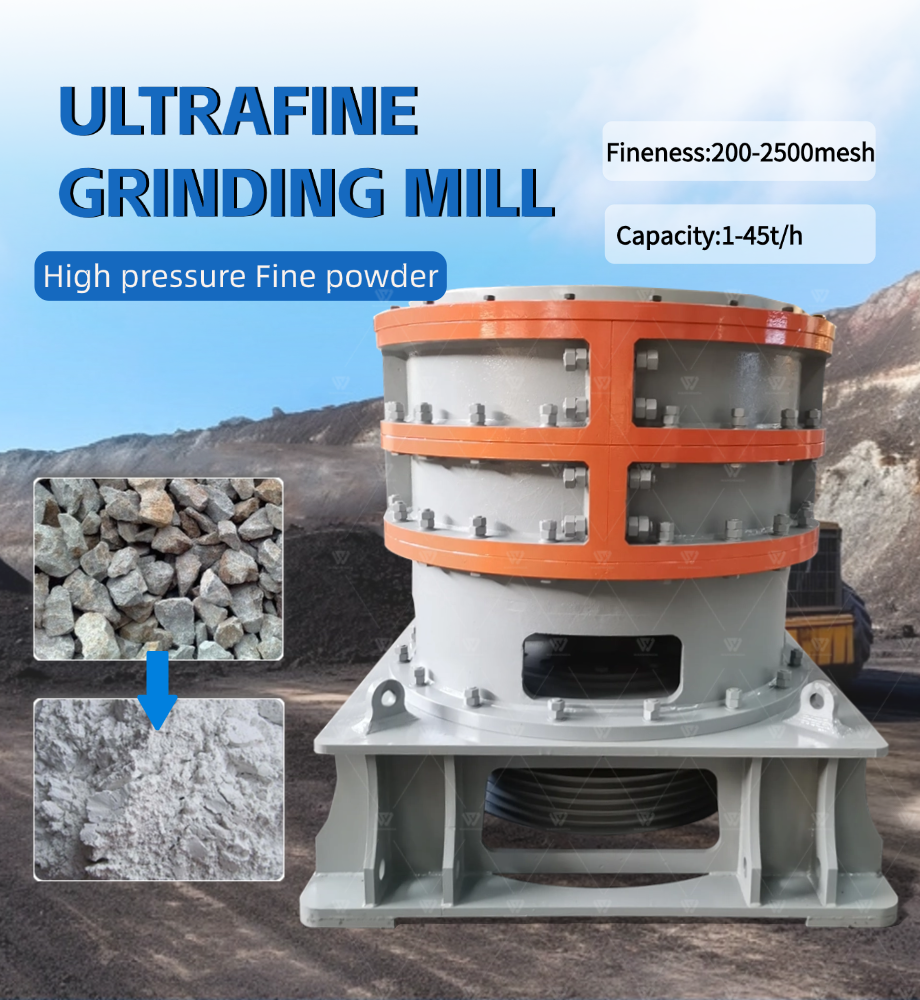
Under the condition of the same finished product fineness and power, the grinding efficiency of the ultrafine grinding mill is 40% higher than that of the airflow mill and the stirring mill, and the energy consumption is reduced by 70%. This high efficiency and energy saving feature makes the ultrafine grinding mill have significant economic benefits in industrial production.
Ultrafine grinding mill is a new type of micro powder and fine powder production equipment, which is widely used in metallurgy, mining, chemical industry, non-metallic minerals, building materials, refractory materials, environmental protection and other industries.
Micro powder grinding is mainly suitable for barite, limestone, calcite, graphite, silicon carbide, quartz, chalk, calcium carbonate, dolomite, kaolin, bentonite, talc, mica, magnesite, illite, pyrophyllite, vermiculite, sepiolite, attapulgite, rectorite, diatomite, barite, gypsum, alunite, graphite, fluorite, phosphate rock, potash ore, pumice, etc.; in addition, it is also widely used in ceramics, coatings, rubber and other industries to improve the quality and performance of products.
Production Line
Raw material was firstly crushed into small particles, and then sent to feeding hopper. With screw feeder, such particles will go into grinder unit and displaced on the upper turn-plate. Turn-plate is turning around the middle axis, and the grinder connects with reducer box, it is driven by the grinder motor. The powders will be grind roller by roller, ring by ring, and fall down on the down turn-plate, and they will go through classifier with the airflow, as the high pressure produces negative wind. All the powder will be classified by the high speed turning classifier impeller. Qualified one will go into collector and filter bags. Big one will fall down and be grind again. Most of the powders will fall into the collector, and few of them will go into bag house with the airflow. With the high pressure, the powder will fall down into screw conveyor and discharged from valve.
Product Parameters
Model |
UGM80 |
UGM100 |
UGM125 |
UGM168 |
Working diameter(mm) |
Φ800 |
Φ1000 |
Φ1250 |
Φ1680 |
Max feed size (mm) |
≤20 |
≤20 |
≤20 |
≤20 |
Final size (mesh) |
200-2500 |
200-2500 |
200-2500 |
200-2500 |
Output (kgh) |
500-4500 |
1000-8500 |
2500-14000 |
5000-25000 |
No.of Roller(PCS) |
21 |
36 |
40-44 |
30-40 |
No.of Ring(PCS) |
3 |
4 |
4 |
4 |
Main Mill(kW) |
55 |
100 |
160 |
|
Classifier(kW) |
18.5 |
37 |
45 |
18.5x5 |
Air Blower(kW) |
45 |
75 |
2x55 |
90x2 |
Screw Conveyor(kW) |
3 |
3 |
2-4 |
2 |
Discharge Valve(kW) |
2x0.75 |
2x0.75x1.1 |
4x1.1 |
1.5x20.75x2 |
Air Compressor(kW) |
7.5 |
15 |
2x15 |
55 |
Product Structure
Long life cycle of spare parts
The ring and roller are forged by special material with high utilization; As no rolling bearings or screws in grinding cavity, there are no problems caused by bolts shedding or rapid wear of bearings and seal components.
High fineness, flexible adjustment
The final fineness of the grinding materials can be adjusted between 200 meshes and 2500 mesh (47-5 micron), and the product fineness can reach D97≤5μm.
Environment friendly
The whole production is equipped with the dust removal system to ensure that the grinding powder is not discharged and the environmental pollution is avoided.
Factory Scene